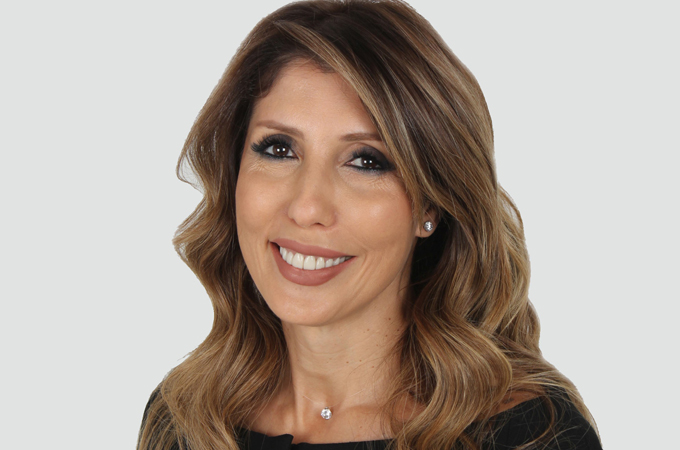
Amel Gardner
Manufacturers need to invest in the `right technology'
DUBAI, April 6, 2020
By Amel Gardner
The term ‘innovation’ can mean different things to different people. No two manufacturing businesses are at the same point in their journey to innovate systems and processes. However, two things that are common on the road to adopting innovative initiatives is budget and resource constraints.
There is no getting away from the fact that no matter what the scale of IT project you are planning to undertake, it will be scrutinised from every budgetary angle and have a big impact on resources—from both an implementation and user acceptance point of view.
Manufacturers are therefore at a crossroads. They understand the need to innovate and invest in artificial intelligence (AI) and other cutting-edge technologies, but the reality is that for many, limited budgets and resources are still a sticking point. Indeed, a survey in 2019 by Ernst & Young in the US found that 42 percent of C-level executives cite a limited budget as their biggest barrier to activating innovative initiatives.
However, figures from March 2020 suggest that Middle East & North Africa (Mena) spending on IT is slowly on the up, despite recent political uncertainty and turmoil. Gartner predicts that IT spend in the region will reach $160 billion in 2020—an increase of 2.4 percent compared to 2019. We are also seeing early adopters within the industry doing some really innovative things within the constraints of a limited budget—proving that it is a hurdle that can be overcome.
For example, Sistema Plastics has maximised its manufacturing outcomes in a pioneering production facility featuring a variety of automation technologies, including robotics and vision recognition systems. By integrating its ERP and manufacturing execution systems, the manufacturer can now connect planning, scheduling and quality data with shop floor realities in one unified system, to drive smarter and optimal working practices.
With the signs pointing to a rise in IT spend and a willingness to innovate, manufacturers need to be able to bridge the gap between the innovation ideal and the reality of investing in the right places. It is easy to get caught up in the excitement promised by AI and robotics to solve skills shortages, or the ability for connected devices to give us the competitive edge, but many manufacturers still don’t know how to approach such an investment to make sure it’s a success. This leaves them wondering just when and how to start.
To make sure manufacturers are investing in the right places, there are some key questions to consider before giving the green light to any technology project.
Does my business need this?
This might seem like a simple question, but every business is different and as such has different requirements and goals. What is right for one organization to remain successful and grow might not be what’s needed for another. Taking on unsuitable technology that doesn’t marry with your internal systems, just for the sake of it, can do more harm than good, and leave companies unable to use it to its full potential.
Is it measurable?
Being transparent and able to show tangible returns will be key to the success of any technology investment. With manufacturers being typically risk-averse, senior executives will expect to see significant reward from any spend made. This is where cloud-based systems are hugely valuable for the sector, as they can enable new systems to get up and running quickly, and often deliver faster returns.
Will it help me delight my customers?
Giving businesses a competitive edge, as well as the ability to retain and grow a customer base, is a key element for any innovative investment. Will it help you get ideas into manufacture more quickly, go to market earlier, trouble-shoot customer queries more effectively, and keep pace with changing customer demands? New systems should enable you to deliver an enhanced customer service level and improve internal efficiencies.
What impact will it have for users?
It’s not just customers that are important to consider—it’s vital to think about the impact that any new technology or process will have on a workforce. Will they feel threatened or empowered? Are there the right skills internally to make adoption a success, as well as a change management plan to ensure users accept it? Working with a third-party expert for implementation and training can help streamline adoption and acceptance.
Can I react quickly enough?
Whether it’s adopting an AI-based system to respond more effectively to customer queries, or adding a new connected sensor to improve visibility of plant production line processes, the ability to innovate and react quickly can only be achieved by taking an agile approach to technology investment.
The past 12 months have shown how political and economic uncertainty has affected the sector, and that flexible and scalable systems such as enterprise resource planning (ERP) must be able to react to current trends, and embrace the unknown. Moving core systems like ERP to the cloud, for example, offers the agility and ability to customise or introduce new products, ramp up capacity, or align supply chains for faster delivery.
Innovative technologies, in whatever form they take, have the power to truly transform processes and outcomes for the manufacturing sector, but only if the fundamental steps to adoption are followed.
About the author
Amel Gardner is regional vice president – Middle East, Africa & India (MEAI), Epicor Software Corp.